From Nothing, Something: One Layer at a Time


A group of engineers working on a novel manufacturing technique at NASA's Langley Research Center in Hampton, Va., have come up with a new twist on the popular old saying about dreaming and doing: "If you can slice it, we can build it."
That's because layers mean everything to the environmentally-friendly construction process called Electron Beam Freeform Fabrication, or EBF3150, and its operation sounds like something straight out of science fiction.
"You start with a drawing of the part you want to build, you push a button, and out comes the part," said Karen Taminger, the technology lead for the Virginia-based research project that is part of NASA's Fundamental Aeronautics Program.
She admits that, on the surface, EBF3 reminds many people of a Star Trek replicator in which, for example, Captain Picard announces out loud, "Tea, Earl Grey, hot." Then there is a brief hum, a flash of light and the stimulating drink appears from a nook in the wall.
In reality, EBF3 works in a vacuum chamber, where an electron beam is focused on a constantly feeding source of metal, which is melted and then applied as called for by a drawing—one layer at a time—on top of a rotating surface until the part is complete.
While the options for using EBF3 are more limited than what science fiction allows, the potential for the process is no less out of this world, with promising relevance in aviation, spaceflight—even the medical community, Taminger said.
Commercial applications for EBF3 are already known and its potential already tested, Taminger said, noting it's possible that, within a few years, some aircraft will be flying with large structural parts made by this process.
To make EBF3 work there are two key requirements: A detailed three-dimensional drawing of the object to be created must be available, and the material the object is to be made from must be compatible for use with an electron beam.
First, the drawing is needed to break up the object into layers, with each cross-section used to guide the electron beam and source of metal in reproducing the object, building it up layer by layer.
"If you take a slice through a typical truss, you can see a couple of dots in each cross-section that move as you go from layer to layer," Taminger said. "When complete, you see those moving dots actually allowed you to build a diagonal brace into the truss."
Second, the material must be compatible with the electron beam so that it can be heated by the stream of energy and briefly turned into liquid form, making aluminum an ideal material to be used, along with other metals.
In fact, the EBF3 can handle two different sources of metal—also called feed stock—at the same time, either by mixing them together into a unique alloy or embedding one material inside another.
The potential use for the latter could include embedding a strand of fiber optic glass inside an aluminum part, enabling the placement of sensors in areas that were impossible before, Taminger said.
While the EBF3 equipment tested on the ground is fairly large and heavy, a smaller version was created and successfully test flown on a NASA jet that is used to provide researchers with brief periods of weightlessness. The next step is to fly a demonstration of the hardware on the International Space Station, Taminger said.
Future lunar base crews could use EBF3 to manufacture spare parts as needed, rather than rely on a supply of parts launched from Earth. Astronauts might be able to mine feed stock from the lunar soil, or even recycle used landing craft stages by melting them.
But the immediate and greatest potential for the process is in the aviation industry where major structural segments of an airliner, or casings for a jet engine, could be manufactured for about $1,000 per pound less than conventional means, Taminger said.
Environmental savings also are made possible by deploying EBF3, she added.
Normally an aircraft builder might start with a 6,000-pound block of titanium and machine it down to a 300-pound part, leaving 5,700 pounds of material that needs to be recycled and using several thousand gallons of cutting fluid used in the process..
"With EBF3 you can build up the same part using only 350 pounds of titanium and machine away just 50 pounds to get the part into its final configuration," Taminger said. "And the EBF3 process uses much less electricity to create the same part."
While initial parts for the aviation industry will be simple shapes, replacing parts already designed, future parts designed from scratch with the EBF3 process in mind could lead to improvements in jet engine efficiency, fuel burn rate and component lifetime.
"There's a lot of power in being able to build up your part layer by layer because you can get internal cavities and complexities that are not possible with machining from a solid block of material," Taminger said.
Watch Karen Taminger's Electron Beam Freeform Fabrication Technical Seminar →
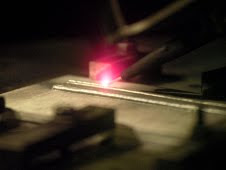
"You start with a drawing of the part you want to build, you push a button, and out comes the part," said Karen Taminger, the technology lead for the Virginia-based research project that is part of NASA's Fundamental Aeronautics Program.
She admits that, on the surface, EBF3 reminds many people of a Star Trek replicator in which, for example, Captain Picard announces out loud, "Tea, Earl Grey, hot." Then there is a brief hum, a flash of light and the stimulating drink appears from a nook in the wall.
In reality, EBF3 works in a vacuum chamber, where an electron beam is focused on a constantly feeding source of metal, which is melted and then applied as called for by a drawing—one layer at a time—on top of a rotating surface until the part is complete.
While the options for using EBF3 are more limited than what science fiction allows, the potential for the process is no less out of this world, with promising relevance in aviation, spaceflight—even the medical community, Taminger said.
Commercial applications for EBF3 are already known and its potential already tested, Taminger said, noting it's possible that, within a few years, some aircraft will be flying with large structural parts made by this process.
To make EBF3 work there are two key requirements: A detailed three-dimensional drawing of the object to be created must be available, and the material the object is to be made from must be compatible for use with an electron beam.
First, the drawing is needed to break up the object into layers, with each cross-section used to guide the electron beam and source of metal in reproducing the object, building it up layer by layer.
"If you take a slice through a typical truss, you can see a couple of dots in each cross-section that move as you go from layer to layer," Taminger said. "When complete, you see those moving dots actually allowed you to build a diagonal brace into the truss."
Second, the material must be compatible with the electron beam so that it can be heated by the stream of energy and briefly turned into liquid form, making aluminum an ideal material to be used, along with other metals.

The potential use for the latter could include embedding a strand of fiber optic glass inside an aluminum part, enabling the placement of sensors in areas that were impossible before, Taminger said.
While the EBF3 equipment tested on the ground is fairly large and heavy, a smaller version was created and successfully test flown on a NASA jet that is used to provide researchers with brief periods of weightlessness. The next step is to fly a demonstration of the hardware on the International Space Station, Taminger said.
Future lunar base crews could use EBF3 to manufacture spare parts as needed, rather than rely on a supply of parts launched from Earth. Astronauts might be able to mine feed stock from the lunar soil, or even recycle used landing craft stages by melting them.
But the immediate and greatest potential for the process is in the aviation industry where major structural segments of an airliner, or casings for a jet engine, could be manufactured for about $1,000 per pound less than conventional means, Taminger said.
Environmental savings also are made possible by deploying EBF3, she added.
Normally an aircraft builder might start with a 6,000-pound block of titanium and machine it down to a 300-pound part, leaving 5,700 pounds of material that needs to be recycled and using several thousand gallons of cutting fluid used in the process..
"With EBF3 you can build up the same part using only 350 pounds of titanium and machine away just 50 pounds to get the part into its final configuration," Taminger said. "And the EBF3 process uses much less electricity to create the same part."
While initial parts for the aviation industry will be simple shapes, replacing parts already designed, future parts designed from scratch with the EBF3 process in mind could lead to improvements in jet engine efficiency, fuel burn rate and component lifetime.
"There's a lot of power in being able to build up your part layer by layer because you can get internal cavities and complexities that are not possible with machining from a solid block of material," Taminger said.
Watch Karen Taminger's Electron Beam Freeform Fabrication Technical Seminar →
0 Response to "From Nothing, Something: One Layer at a Time"
Post a Comment